Mfg - An Overviews
Wiki Article
Top Guidelines Of Manufacturing
Table of ContentsA Biased View of Additive ManufacturingLittle Known Questions About Manufacturing.Fascination About Plastic ManufacturingMore About Hon Hai PrecisionThe Ultimate Guide To ManufacturingGetting My Lean Production To Work
The text on this page is an example from our full White Paper 'Injection Moulding for Customers' - * Example text * - for full guide click the download button over! Introduction This overview is planned for people that are aiming to resource plastic mouldings. It provides a much required understanding right into all that is entailed with producing plastic components, from the mould tool needed to the moulding procedure itself.If you desire to explore even more, the overview covers sorts of mould devices, as well as special completing processes such as colours & plating. Words that are highlighted can be found in the reference in the appendix ... Part I: Moulding: The Basics The Benefits of Shot Moulding Plastic injection moulding is a very precise process that provides a number of advantages over other plastic handling techniques.
Accuracy is excellent for really detailed components. You can hold this moulding in the hand of your hand as well as it has employers, ribs, steel inserts, side cores and also openings, made with a gliding shut off attribute in the mould device.
What Does Plastic Manufacturing Mean?

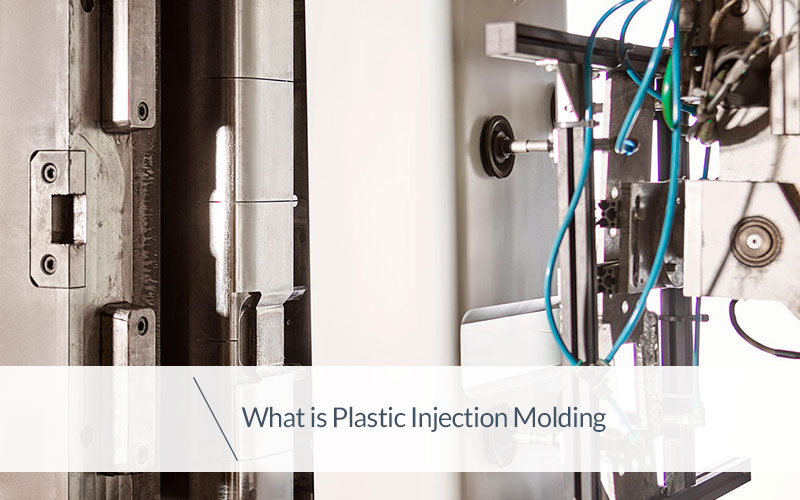
from material feed Product melting; material injectionProduct shot time and ejection as well as the re-closing of the mould tool ready for prepared next cycleFollowing Draft angles - The wall surfaces of a moulded component must be a little tapered in the direction in which the component is expelled from the mould device, to permit the part to be ejected conveniently.
Ejector stroke - The pressing out of ejector pins to expel the moulded component from the mould device. Ejector stroke rate, length as well as timing requires to be thoroughly regulated to avoid damages to the ejectors as well as mould device, however at the same time make the moulding cycle as brief as possible.
official website
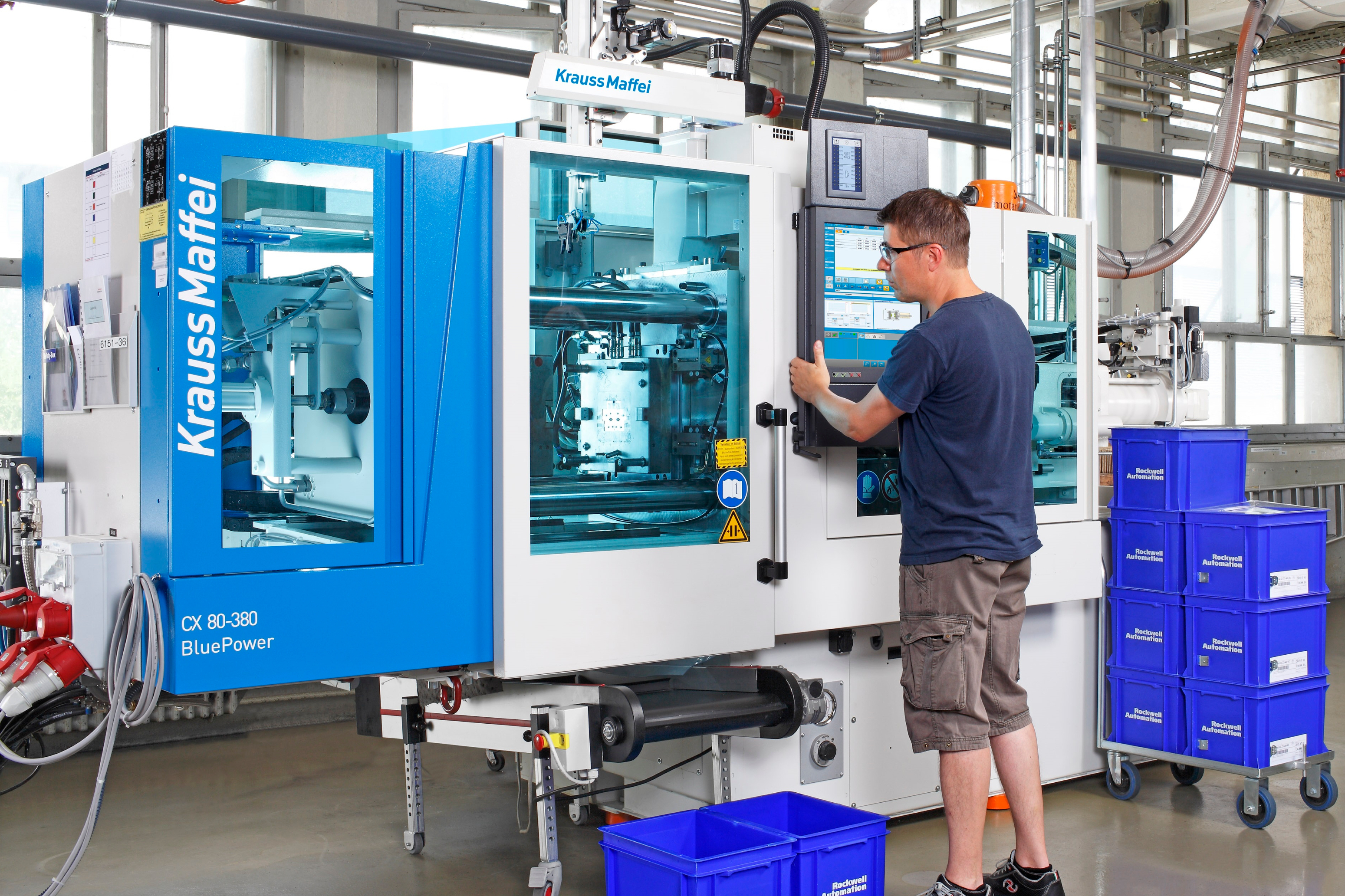
Lean Production - The Facts
Ribs - When a plastic part see this page has slim walls, ribs are contributed to the style to make the slim wall surfaces more powerful Side cores - Side activity which produces an attribute on a moulded component, at an opposing angle to the regular opening instructions of the mould device. additive manufacturing. The side core requires to be able to pull back as the plastic component can not be ejected otherwise.
Walls - The sides of a moulded component The message on this web page is an example from our complete White Paper 'Injection Moulding for Customers'.
Shot moulding is widely utilized for making a range of parts, from the smallest elements to entire body panels of autos. Shot moulding utilizes a special-purpose maker that has three components: the injection unit, the mould and also the clamp.
Getting My Additive Manufacturing To Work
Refine features [modify] Injection moulding makes use of a ram or screw-type plunger to require molten plastic or rubber material right into a i thought about this mould cavity; this solidifies into a form that has satisfied the contour of the mould. It is most frequently utilized to process both thermoplastic and thermosetting polymers, with the volume use the previous being considerably higher.: 13 Thermoplastics are widespread due to characteristics that make them extremely suitable for injection moulding, such as simplicity of recycling, adaptability for a vast selection of applications,: 89 and capacity to soften and also move on heating.In several tooth cavity moulds, each cavity can be the same and develop the exact same parts or can be special and form several various geometries throughout a solitary cycle.
The screw delivers the raw material forward, blends and homogenises the thermal as well as thick circulations of the polymer, as well as decreases the called for heating time by mechanically shearing the product as well as including a significant amount of frictional heating to the polymer. The product feeds ahead via a check valve and gathers at the front of the screw into a quantity referred to as a shot. When sufficient material has gathered, the product is required at high pressure and rate into the component creating dental caries. The specific quantity of contraction is a function of the resin being utilized, and can be reasonably predictable. To avoid spikes in stress, the process typically utilizes a transfer position corresponding to a 9598% complete tooth cavity where the screw changes from a consistent rate to a constant stress control.
All about Manufacturing Industries
The packaging stress is applied up until the entrance (dental caries entry) strengthens. Due to its tiny dimension, the gate is usually the first place to strengthen through its whole thickness.: 16 Once the gate strengthens, no even more product can get in the dental caries; as necessary, the screw reciprocates and also obtains material for the following cycle while the product within the mould cools so that it can be ejected as well as be dimensionally steady.Report this wiki page